編按:「大企業病」讓流程繁瑣、決策遲滯,影響企業效率。《精實法則》透過自行車零組件廠的案例,解析 「時間差管理」,並透過資訊流優化、並聯作業、即時排程調整,減少決策延遲與執行落差。文章進一步探討精實管理在生產現場、供應鏈、電商倉儲的應用,幫助企業靈活應對市場變化。對於企業經營者與管理者來說,這篇書摘提供了實用的改善策略。
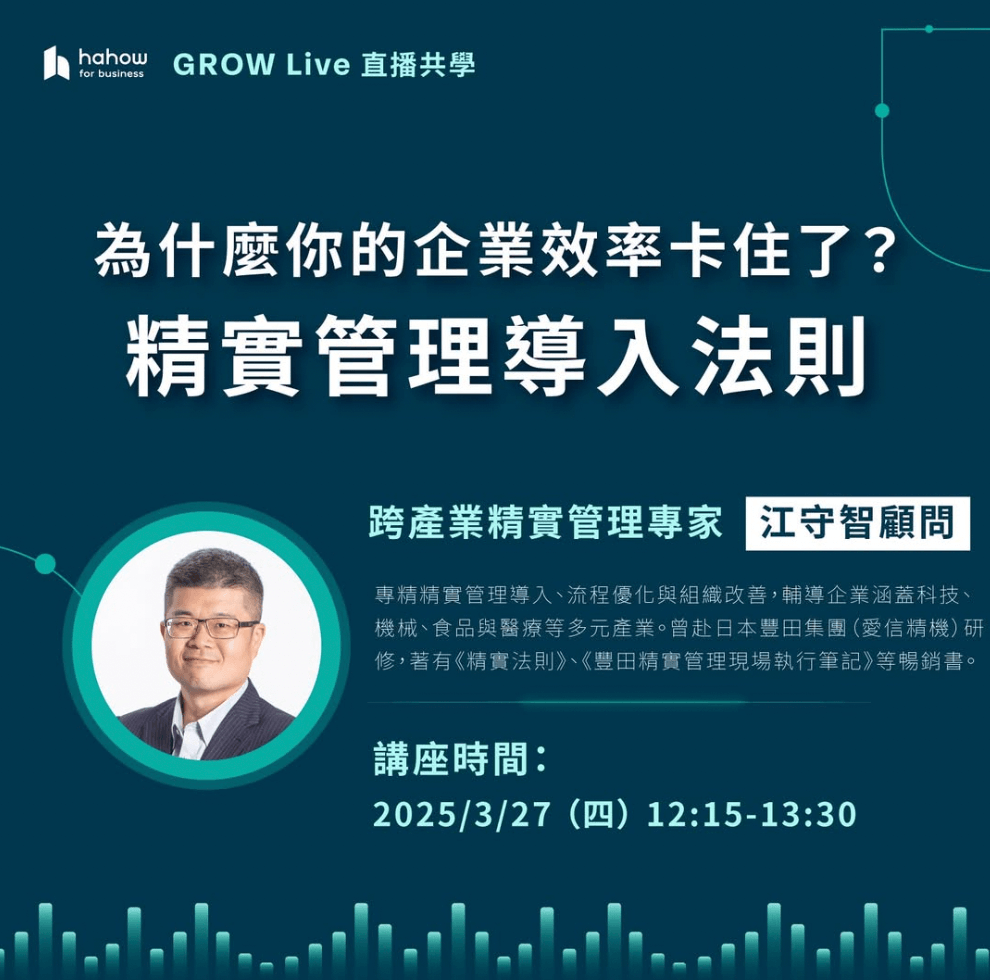
📢 GROW Live 直播講座|你的企業效率卡住了嗎?精實管理導入法則
企業推動精實管理時,常遇流程卡關、數據無改善、員工抗拒變革,導致管理流於形式,影響營運成效。如何讓精實管理真正落地,提升效率並優化成本?
3月27日,江守智老師(本文作者)將透過台灣企業成功案例,拆解 流程改善、問題分析、成本控管 的落地法則,幫助管理者掌握可執行的策略與工具。
- 時間:2025/3/27(四)12:15-13:30
- 適合對象:企業決策層、管理者、HR、供應鏈與品質管理人員
免費預約報名,掌握高效管理關鍵!👉 https://bit.ly/4i9nrD7
我還記得我第一次聽到「大企業病」這個名詞,是與日本顧問一同在上海某企業輔導時所提及,老人家針對兩個議題不斷詢問,一是要修改射出成型模具讓換線時間加快,二是備料人員從倉庫改成隸屬製造單位使需求情報更快傳遞。
結果過了一個月,改善團隊的回覆依然是「關於模具的修改,我們要請業務單位跟客戶端進行確認,內部研發也說要再評估會不會讓毛邊增加。」、「目前備料人員共有八位,我們協理說牽涉到倉庫跟生產單位的人力調整,要跟副總確認才行。」
聽完解釋後,老人家氣得在會議室白板寫下「大企業病」四個字,提醒大家注意以下這幾種情況:
- 公司部門多,例如一個課長底下只管 10 個人,你是國軍班長嗎?
- 職責分不清,這件事不歸我管也不歸他管,就這麼剛好是德州安打嗎?
- 決策耗時長,遇事不決就量子力學嗎?沒有,是層層上報。
- 不願改現況,我還以為我在看清宮劇裡的大臣在殿上爭論「祖宗家法不可變」。
結果又過了幾年,我反而發現所謂的「大企業病」蔓延得很快呢!原本以為可能像是克萊斯勒、通用電器、三星電子等公司如同商管教科書裡的案例,結果台灣中小企業竟然也越來越相似,之所以要特別寫下這篇來提醒,是因為根據經濟部中小及新創企業署發布的《2023 年中小企業白皮書》提到,在 2022 年台灣中小企業家數超過163 萬家,佔全體企業數的 98.9%,而就業人數為 913.2 萬人,佔全台就業人數的八成。如果大企業病愈發蔓延,對台灣整體經濟發展絕對不是件好事。
直接、間接單位的流程管理:用時間來觀察並改善
在大甲工業區裡,自行車零組件業的生管單位想要進行流程改善,除了物流之外,資訊流也是很重要的一部分。然而大家所提出的改善往往只針對單一作業面如何縮減時間,結果發現效益不大。我建議大家可以先以傳統流程圖進行體檢:
傳統流程圖上常見的三種符號:
■ 作業處理
◆ 檢驗確認
⮕ 流程方向
而我卻認為在實務上有個無法克服的缺陷,那就是「停滯等待時間」無法顯現。這就使得我們無法確切瞭解流程時間,除非特別去觀測紀錄。但為什麼我們需要特別去紀錄作業時間、檢驗確認時間、傳遞時間與「停滯時間」呢?因為玩的就是真實,同時也能讓我們瞭解可以改善的切入點。
✎ 停滯時間:情報傳遞/供給頻率
寄出不等於收到,告知不等於知道,情報傳遞上如果射後不理,很有可能最後造成重大延遲而不自知。
我最喜歡舉的例子就是郵差跟宅急便,郵差如果寄平信就是把信丟到郵箱裡,至於你有沒有收到,那不是他的責任;但宅急便可就不一樣,會要求客戶一定要簽收才會離開。這就是情報傳遞需要注意的細節,更關乎我們的管理流程如何設計。
想像一下整堆公文壓在你同事桌上的畫面,明明批完、簽完為什麼還不往下一個處室送呢?「我都習慣一整天整理好後再送出。」恭喜你!這就是供給頻率造成的停滯時間。把供給頻率拉高,例如一天送件兩次,就能夠減少產品、文件、專案的停滯時間。更重要的是如果不是實體製造流程,你的搬運成本更低,何樂而不為呢?
✎ 作業時間:分工方式/改善優化
原本一個人工作要花 60 分鐘,分給兩個人反而只需各花 25 分鐘,那是因為有可能減少移動、反覆拿取工具的結果。又或者原本三人作業因為分工不平均造成等待或庫存堆積問題,但如果平準化分工會讓作業效率變的更快更好。
改善優化就沒有什麼好說,在實體製造作業的改善,不管是物料擺放位置、作業順率、工具手法都可以細究改善。在流程管理時,伴隨著科技的進步,有更多簡單、方便且售價持續降低的AI 自動化工具都是可以檢討使用的途徑。
✎ 移動時間:串改並聯/情報共有
既然是流程改善,可以想像絕大多數的流程圖繪製方式都是「一關接著一關」,彷彿串聯的電路圖一樣。那如果我們把串聯改成並聯,是否就可以大幅減少流程 L/T 時間呢?這概念就像是豐田汽車在設計開發時很常採用的「同步工程」,讓前後流程間緊密結合。
除了物流上的串聯改並聯外,資訊流的情報共有平台也是另外一種減少移動時間的做法。這部分隨著通訊軟體的發達,在情報共有化上起了非常大的作用,例如企業工作用的 Line 群組就是最好的例子。惟要注意資訊的寄出是否等同於收到這件事(請參考上面的停滯時間)。
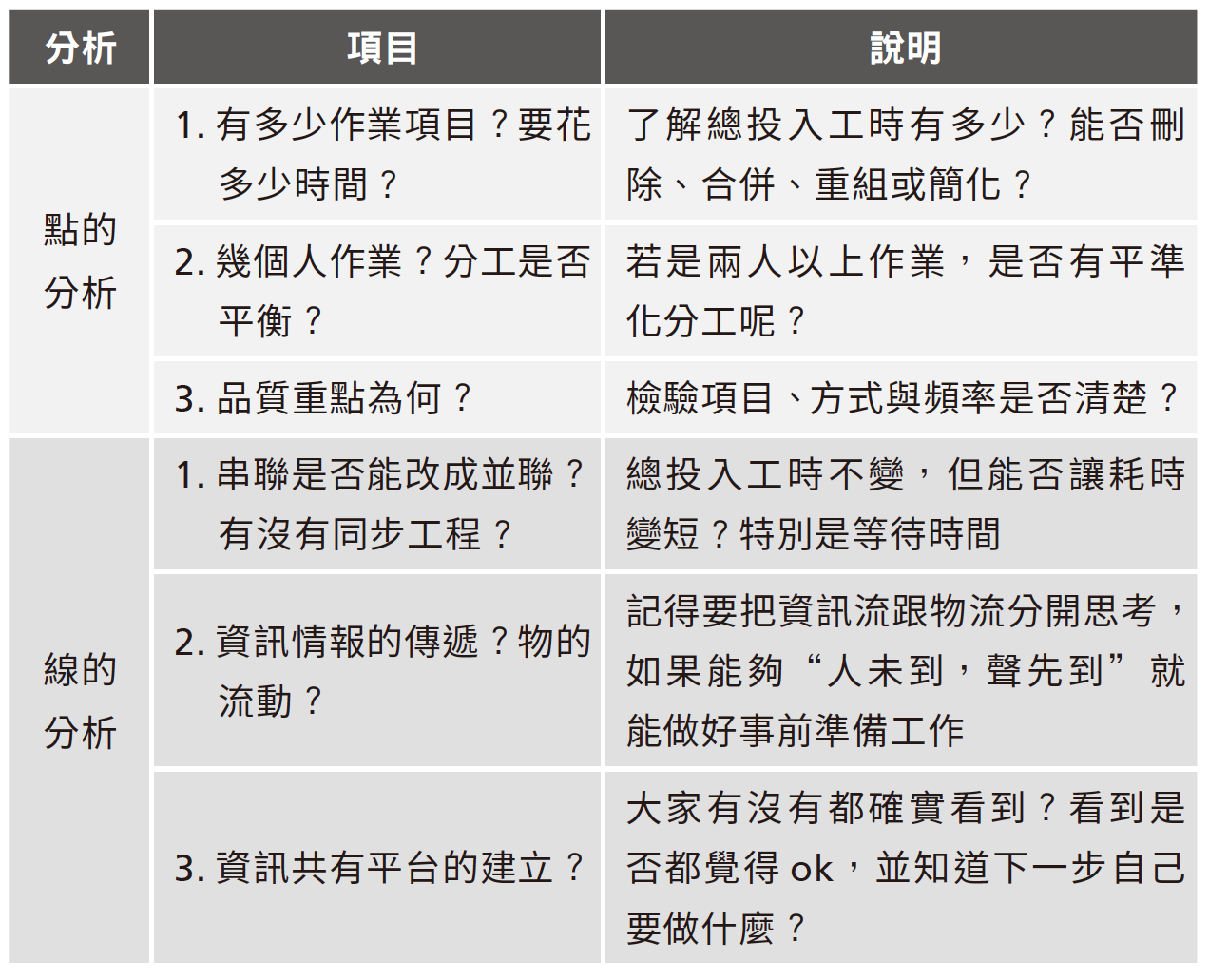
我會建議大家要先做「點的流程分析」,再來做「線的流程分析」,因為從自己本身作業改善起,比較有說服力。另外單點改善著重在投入工時的優化,這是最根本也閃不了的基本功,請務必好好面對。
改善團隊有人舉手發問:「老師,有沒有可能先做點、再來線,最後又回去做點的改善?」很棒的問題,這一定是有思考或親身經歷過才問出。我的答案是當然有可能,而且這樣更好。我的理由有三個:
- 先做點,再串線,會讓前後兩點距離更近。
- 距離變近,前後工序間就更好反映問題或困難。
- 回頭做點的改善就不只是自己視角,更有前後方的視角想法。
直接、間接單位的異常管理:小批量情報供給
在智慧機械聚落的潭雅神六公里產業聚落,J 公司是專門從事齒輪車床加工、機械零配件加工的小公司,公司人數在十人以下卻臥虎藏龍的小而美企業。
總經理說公司的生管跟製造現場常有衝突爭吵,生管人員在排程時認為「你們應該要這樣做」,但製造端反而會認為「但我們覺得這樣比較好」,改善的重點是生管要更瞭解製造的難處、考量點,寫成守則,定期追蹤回饋並修正。
幾個重點一一跟大家分析如下。
✎ 排程臨時更動讓生管、製造都滿腹怨言?
那為什麼生管需要一口氣把整天的排程先提供給製造?我建議只給現場三個情報資訊:
- 現在要做什麼產品?
- 要做多久?做多少量?
- 下一個要做什麼產品?
給現場越單純、越小批量的情報,把變動的可能攔截在生管這邊就好。
過早把生產情報提供給製造單位,製造單位可能就會藉此先拿去備料、預組裝,甚至變更製程先做簡單但並非當下需要的東西。這也是精實管理中的小批量多回次概念,不只運用在物的流動,情報流也需要。
✎ 現場進度或問題,生管在辦公室不見得了解?
在會議討論的當下,J 公司的生管人員說:「我們怎麼會知道現場在做什麼?」聽到當下我也老大不高興地說:「你當你們公司是多大,你就坐在二樓吹冷氣,走個樓梯下樓看一下或問一下很難嗎?」
我會建議可以用「生產管理板」揭露現場資訊,雖然不到即時,但至少只有一小時的時間差。上面白板的資訊包含時段別、產品名稱、預計該時段目標量、該時段實際生產量及備註。由產線組長每小時填寫一次,生管也應該每小時巡檢一次。其目的:
- 即時瞭解生產進度,是否有需要調整、補救的對應?
- 收集未達標的原因,作為後續改善參考。
- 穩定達標者,作為後續目標修正的參考。
✎ 不將就才不會照舊:盯緊產品生命週期
改善目標要怎麼訂才能夠讓公司內部單位可以槍口一致對外。不管是客戶端固定每年合理化要求,抑或是公司對於整體接單情況或市場情勢判斷,都不要忘記「時間差」的問題,你終究是要買歐洲車的... 阿不是,我是說你終究是要做改善的,越早產出效益就會享有更多的紅利,特別是有生命週期的產品更要注意。
即便同樣是機械業,但客戶對於訂單的需求、物料供給情況以及人員的多能工能力,就會成為改善的前提條件,影響接下來我們能做的事情。同時更要看公司對於未來策略方向的選擇,有些產品如果不在公司未來三五年的規劃藍圖中,那麼現階段的改善就會選擇「維持不惡化」不投入過多資源在其身上。
「我們要在量產第一天就賺錢。」這不會是口號,端看我們從產品設計、模擬試做、小批量產的著力多寡?如果你產品生命週期是四年,那你可能還有前半年可以調整修正,但產品生產週期兩年可能就要在兩個月內翻正。在現在少量多樣、推陳出新速度極快的市場環境下,量產第一天就要賺錢這件事真的不是口號。
例如在清潔用品的製造現場,我們有看到一個問題就是新品試車的混亂。生管一開始在途層設計安排五人負責生產,可是現場實際測試時用六人作業。原來是因為貼標籤在瓶裝產品的位置不正,所以增設一員因應。這些我都懂也可以接受,但既然是新產品,當天試車完後我們怎麼檢討?有沒有後續修正想法?下一次想法怎麼落實?這些才是我想傳達的重點。
同樣的問題,針對電商倉儲與特賣會場地整併一事,由於時間關係,公司決定先把特賣會揀貨地點移至新場地,待第四季時再將電商倉儲併入。如果你讓我選擇的話,我會說:If not now, when?(如果不是現在,那要等待何時?)因為兩次搬遷的痛,不如痛一次就好。
生管單位詢問:「如果以過去三年的平均來推估接下來雙11檔期的需求量,會有困擾。」因為訂太少可能會補貨不及,但如果訂太多怕是檔期過後的生產線會有一段真空期。我的回覆有三個重點:
- 處於持續成長或下滑階段,用平均不準。
- 預估就要多跟外界接觸市場情況,總體經濟情況、產業發展趨勢等。
- 預估終究會有失準的可能,其實關鍵在於「生產能力」。
單位時間內擁有夠強的生產能力,就可以不用過早生產備庫存,面對變化的能力也變強。而生產能力的瓶頸在哪,我們改善就應該到哪!
設計規劃、初期檢討才是影響每一項產品獲利與否的關鍵時刻,急就章的「將就」到後來就會變成「照舊」,然後效益不如預期時才想要「搶救」,但又有更新的任務出現就不了了之。想突破這樣的惡性循環,我們就從今天開始做好設計規劃跟初期檢討吧!
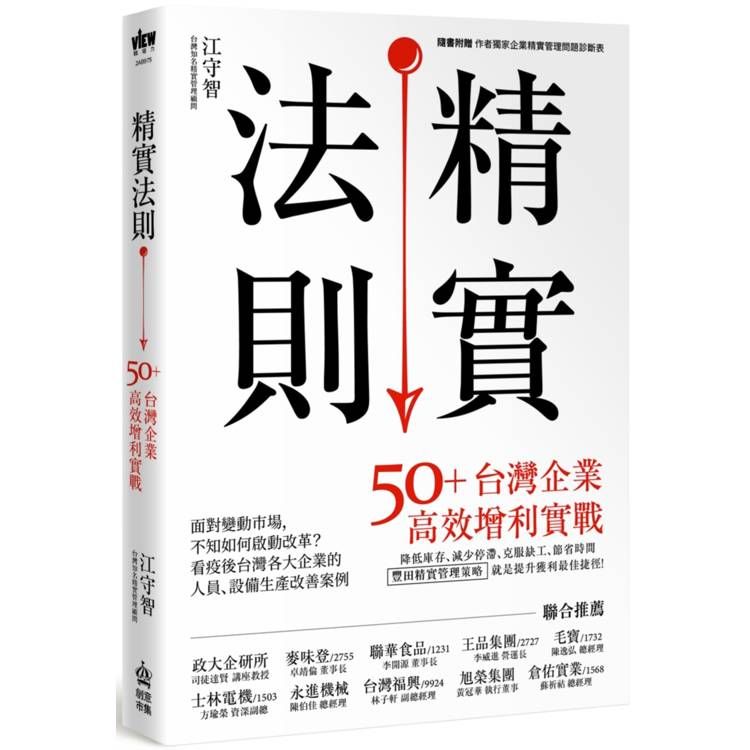
- 書名/精實法則:50+台灣企業高效增利實戰
- 作者/江守智
- 出版社/創意市集
- 出版日/2025 年 2 月 22 日